soundcollage
Well-known member
- Joined
- Dec 11, 2007
- Messages
- 71
Greetings everyone, and thank you the wealth of information you have provided me with. I am an infrequent poster but i have been paging through everyone's posts for at least five years now. I finally have both a camera and a hosting account so I figured I'd post some photos of the projects you've unknowingly helped me complete. I just completed a marathon session of three simultaneous projects: an eight channel api 312, a silent arts dla2a, and a pultec peq/meq combo. I'll start with the 8312 in this post and add projects in subsequent posts so i don't get confused with too many links in a post. extra special thanks to classic api for the amazing parts.
I designed my own boards for this- no phase or pad as I have specific reverse phase cables I made and in line pads if needed
Into the cupric chloride, I grabbed the boards from the wrong pile so they were 3oz copper which i figured out after the 6 hour etch time.
I worked off the gdiy 51x power supply schematic but 'isolated' each feed with its own 1k resistor/10µ cap.
didn't check the size of the caps i had on hand before the layout so had to sneak a few in on the bottom
all traced end up tinned. with the 3oz copper these end up massive.
the first two channels have 24 pos gain switches, direct ins with pikatron transformers, and t-pad output attenuators.
par metal case and gdiy toroid
i have cutting square holes so i mounted the 2503's on standoffs
front panel silkscreened next to dla2a which i crammed on the same screen (I promised a silkscreen tutorial to someone, I'll get to that in a subsequent post in this thread)
front panel drilled and illuminated phantom switched wired in. my only 'oops' in this project was forgetting about the front lip in the par metal case- i had to sawmill across the front to clear the xlr's
doa boards from classic api, but i sourced the parts myself only took 90 transistors to find 8 matching pairs
tight fit
finished (I've since got smaller blue versions of the red knobs for the trim pots on the first two channels)
I designed my own boards for this- no phase or pad as I have specific reverse phase cables I made and in line pads if needed


Into the cupric chloride, I grabbed the boards from the wrong pile so they were 3oz copper which i figured out after the 6 hour etch time.

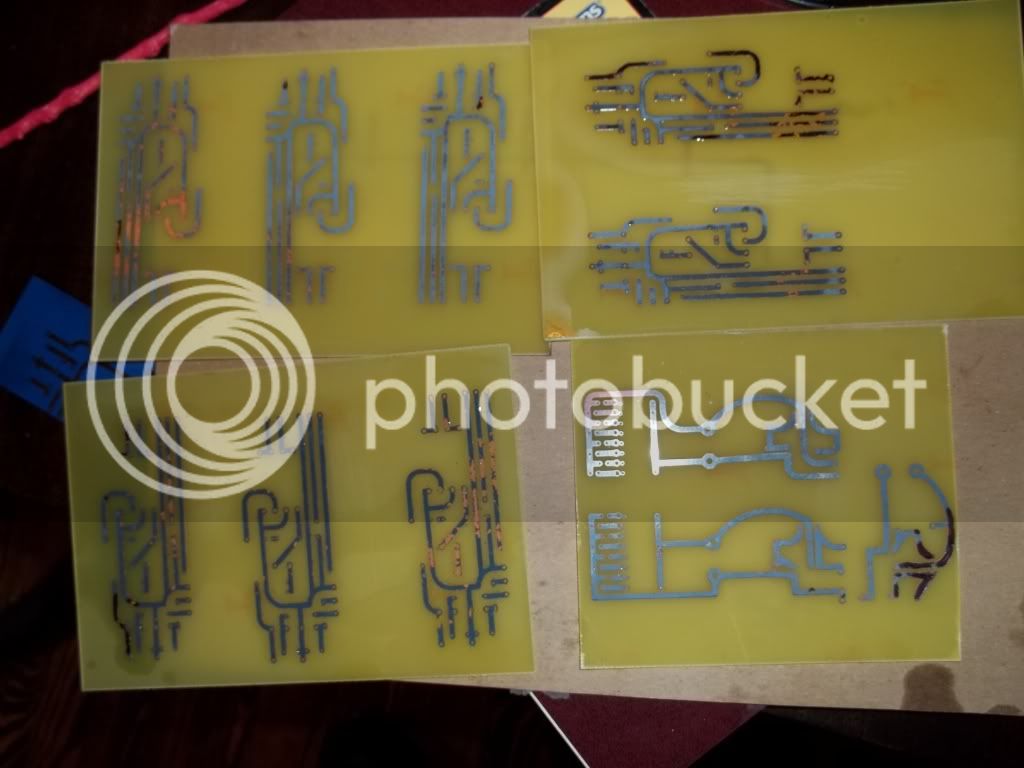
I worked off the gdiy 51x power supply schematic but 'isolated' each feed with its own 1k resistor/10µ cap.

didn't check the size of the caps i had on hand before the layout so had to sneak a few in on the bottom
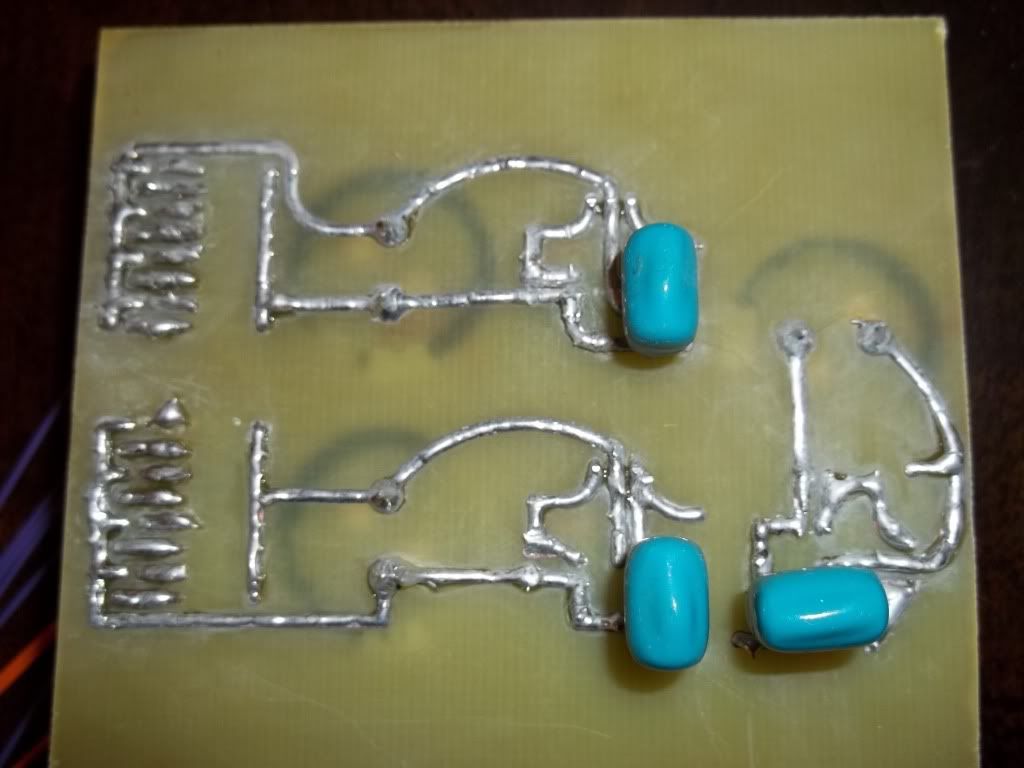

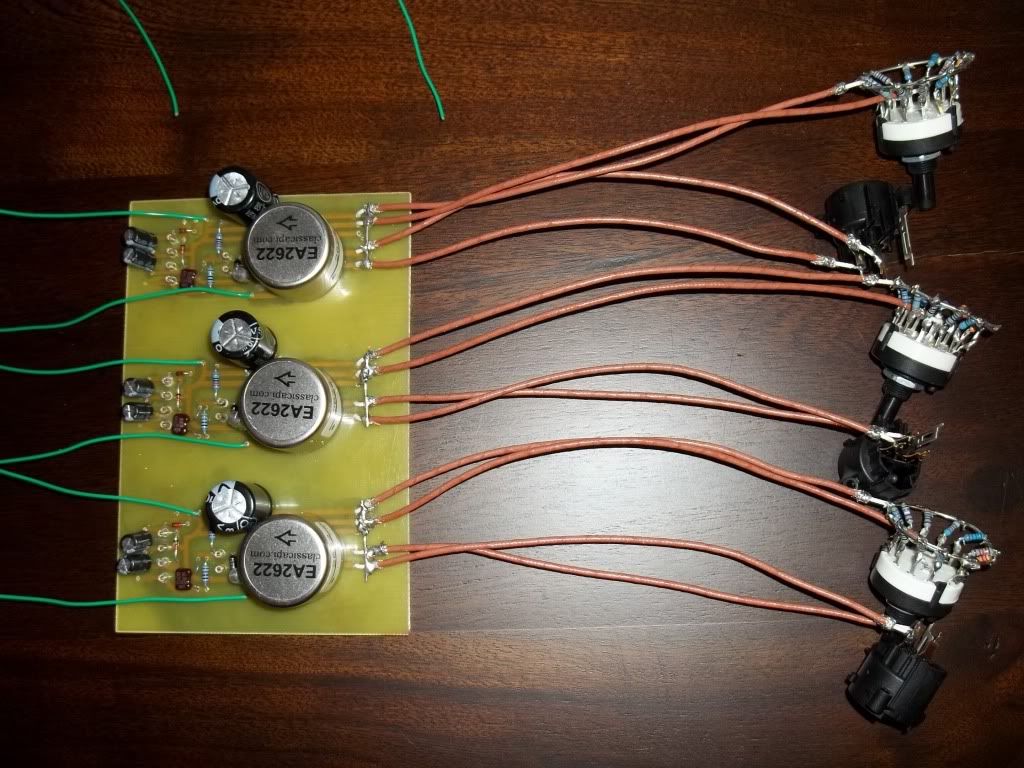
all traced end up tinned. with the 3oz copper these end up massive.
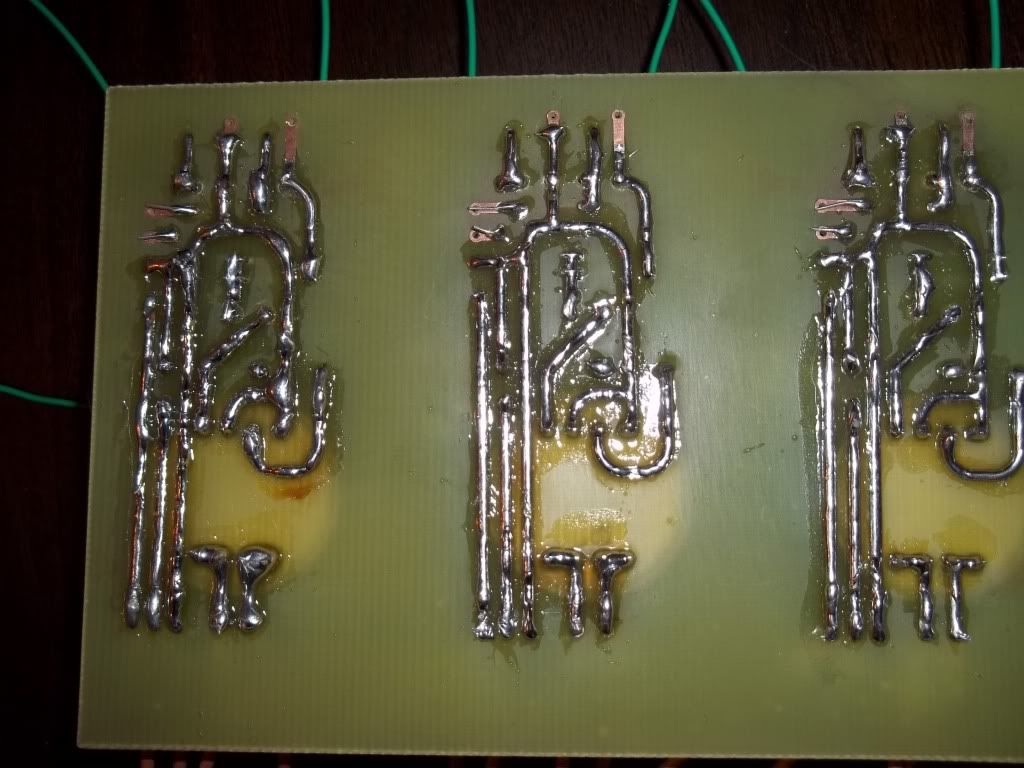
the first two channels have 24 pos gain switches, direct ins with pikatron transformers, and t-pad output attenuators.
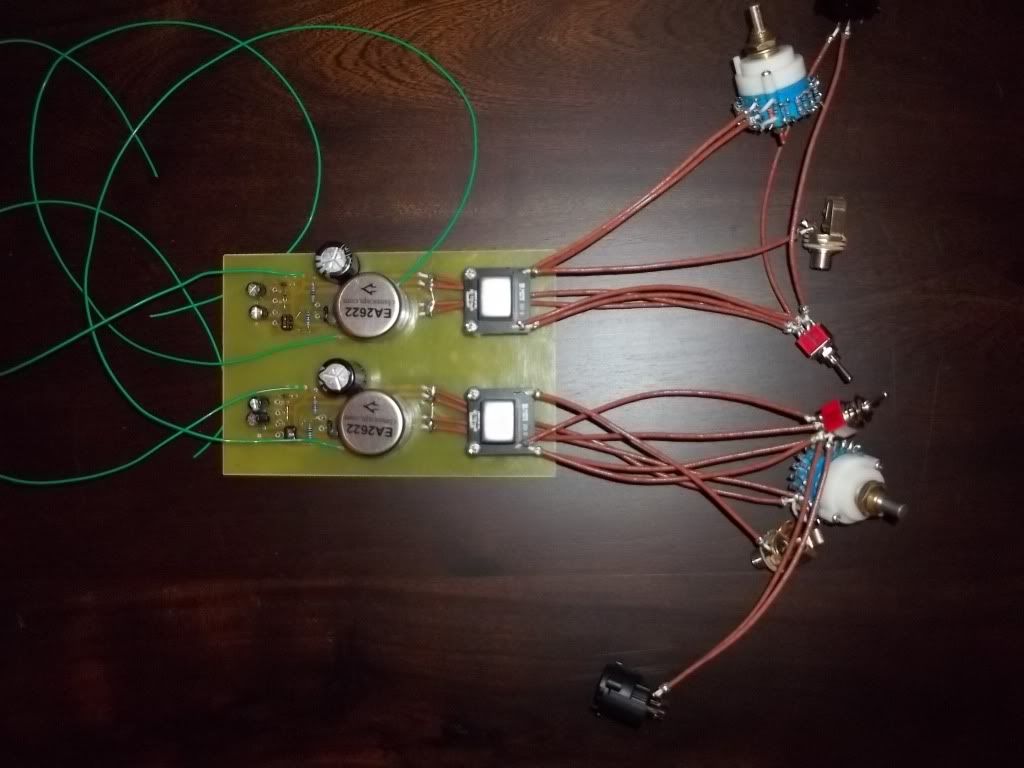
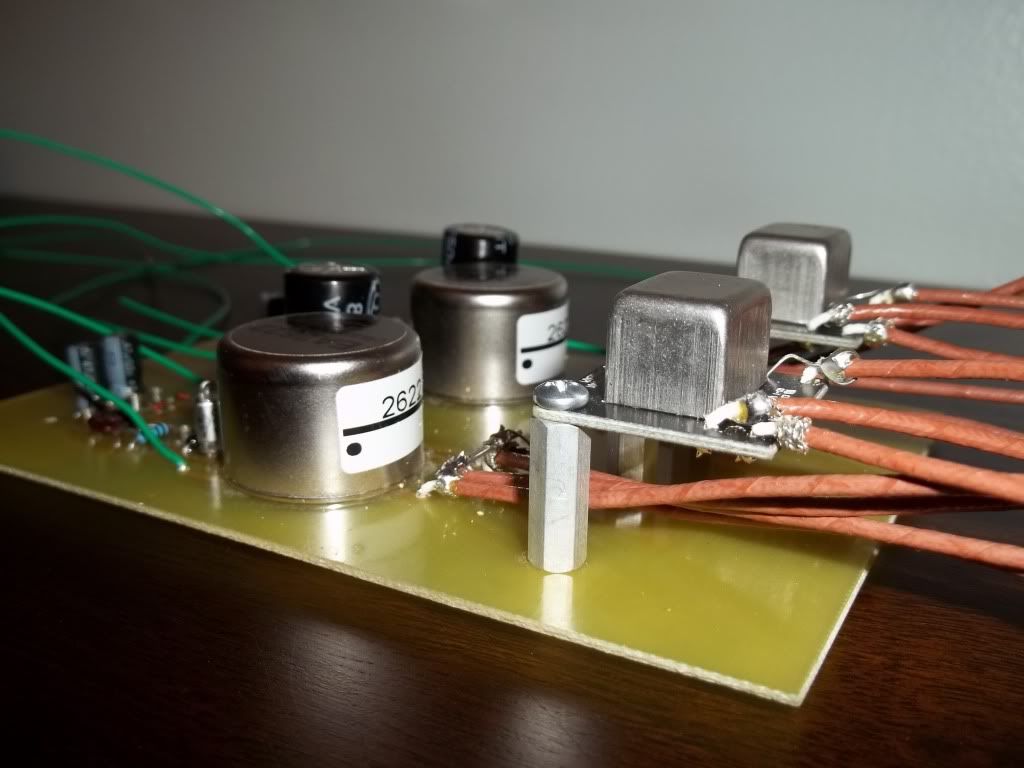

par metal case and gdiy toroid

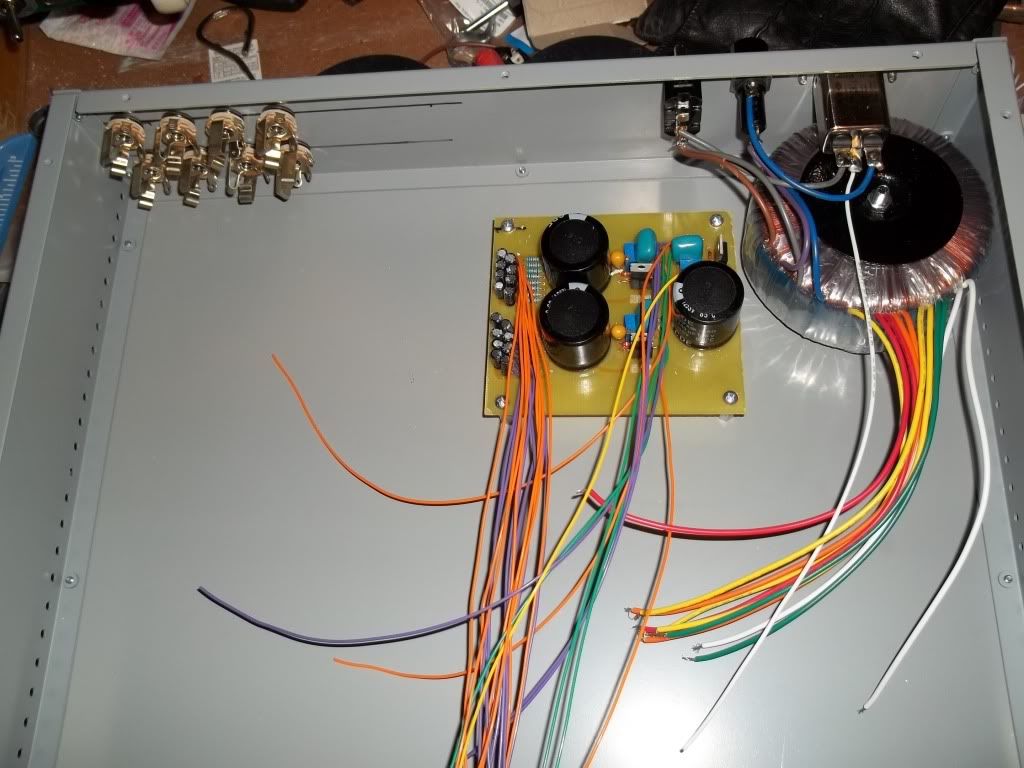
i have cutting square holes so i mounted the 2503's on standoffs
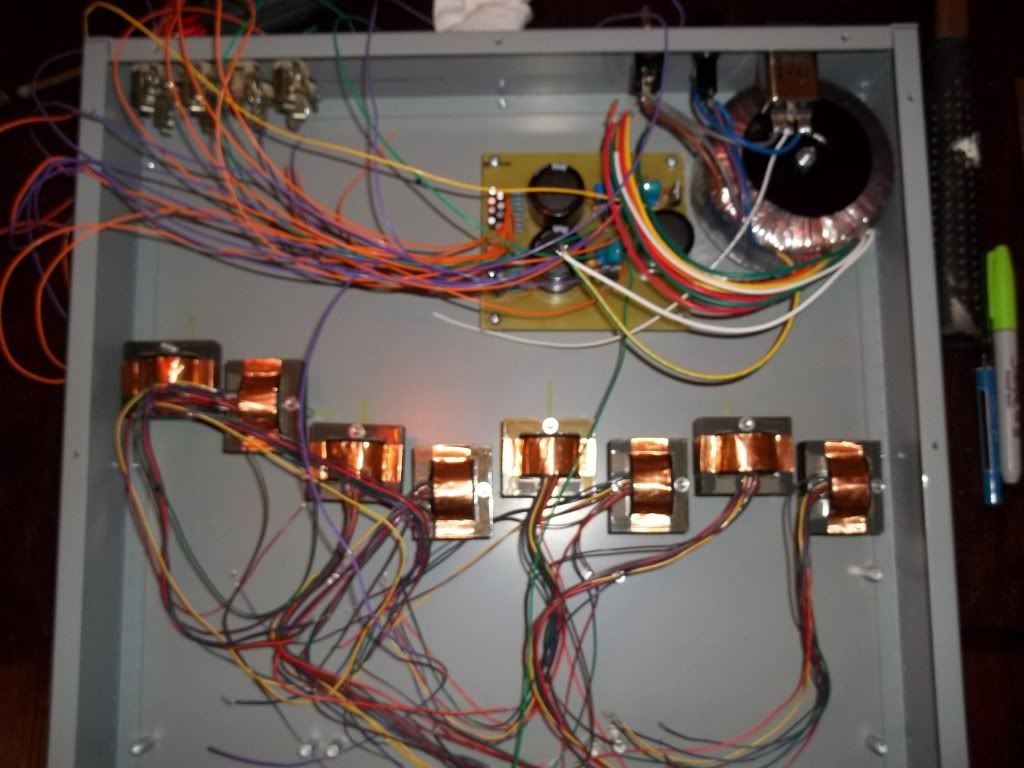
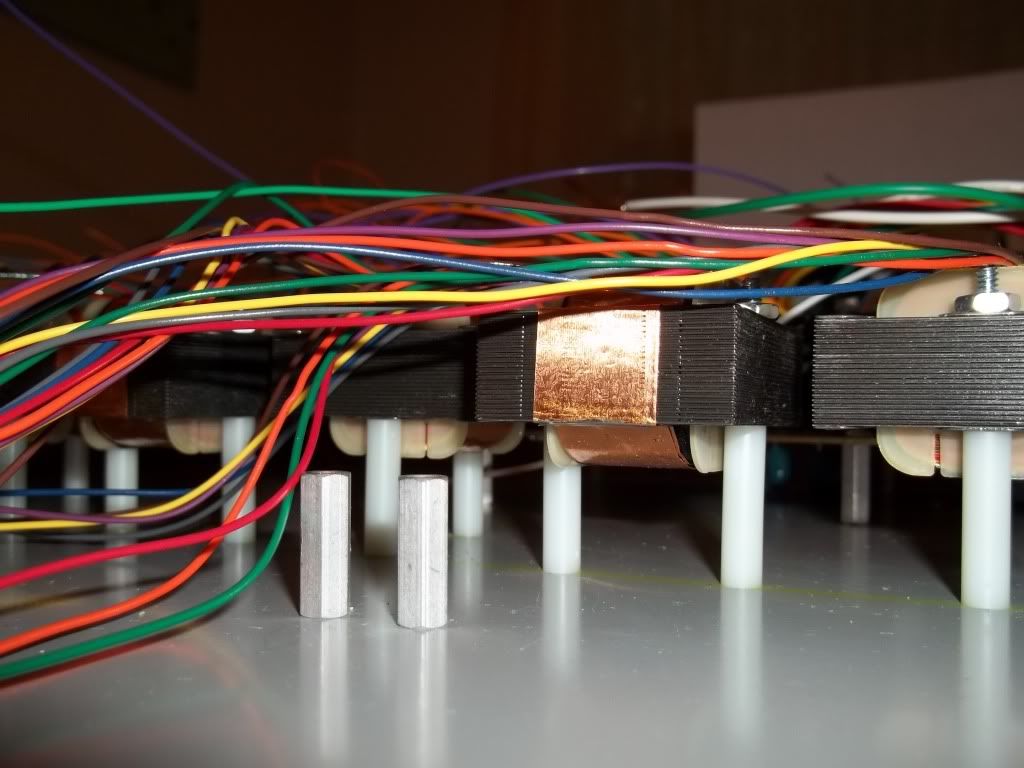
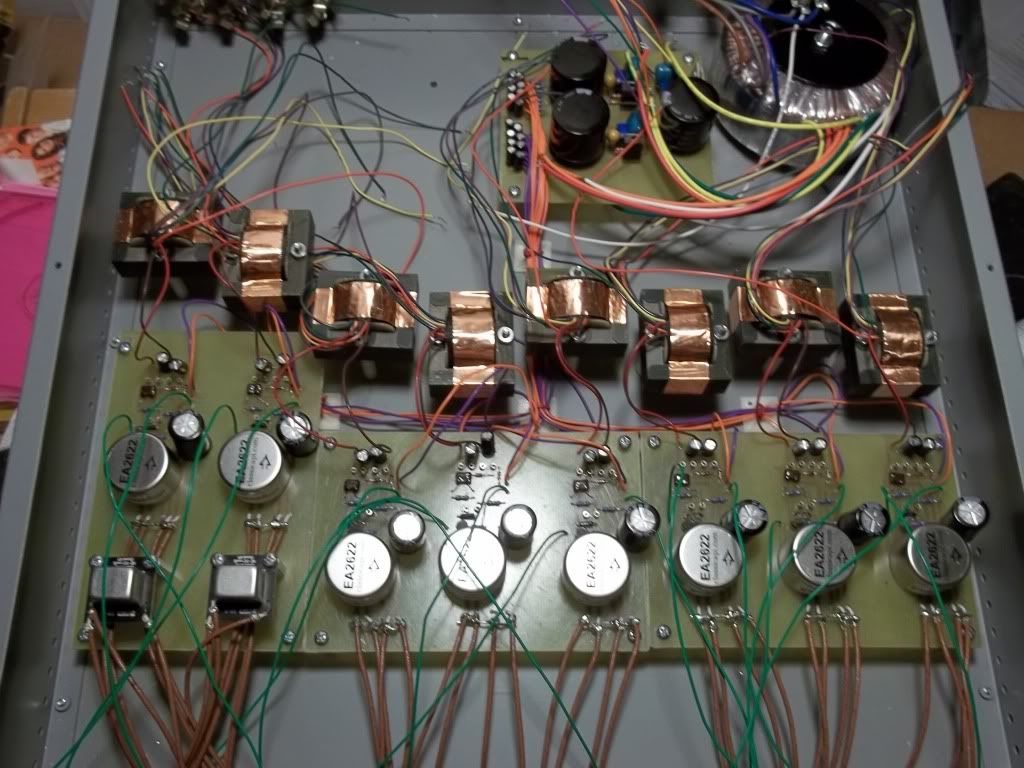

front panel silkscreened next to dla2a which i crammed on the same screen (I promised a silkscreen tutorial to someone, I'll get to that in a subsequent post in this thread)

front panel drilled and illuminated phantom switched wired in. my only 'oops' in this project was forgetting about the front lip in the par metal case- i had to sawmill across the front to clear the xlr's
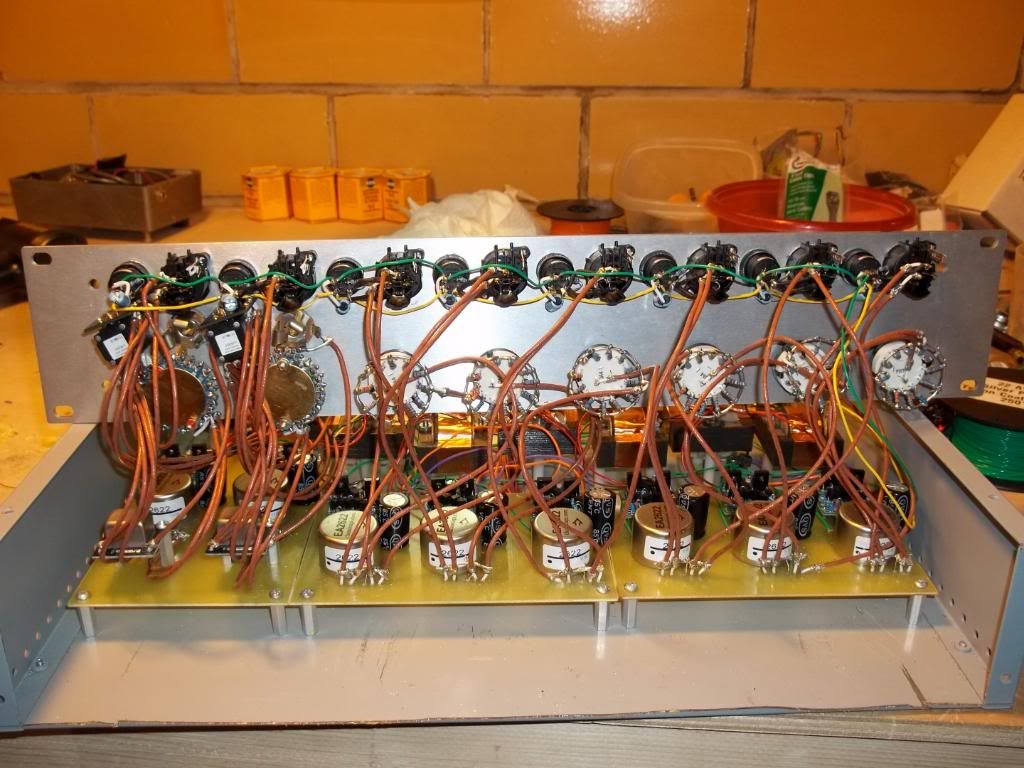
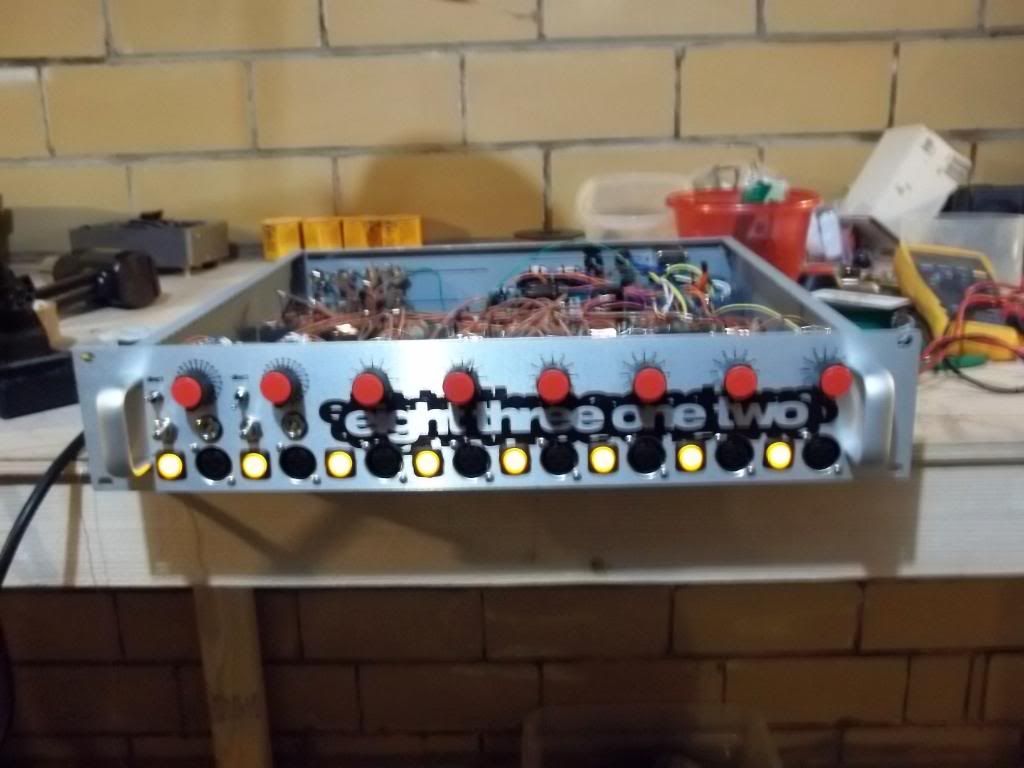
doa boards from classic api, but i sourced the parts myself only took 90 transistors to find 8 matching pairs

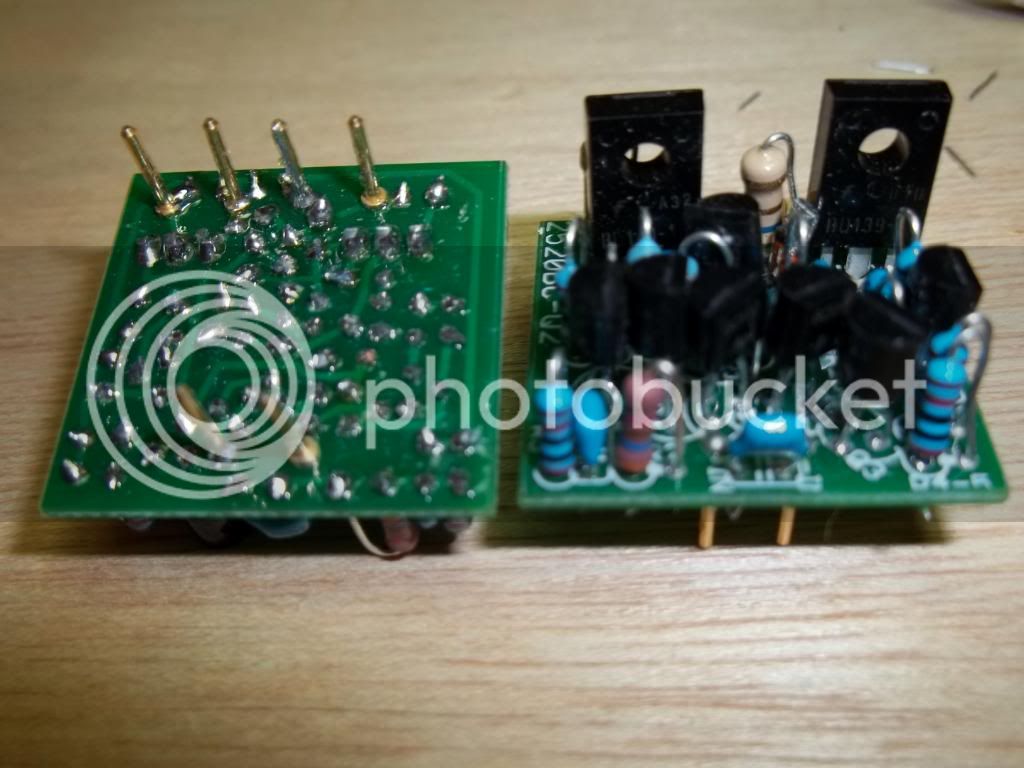
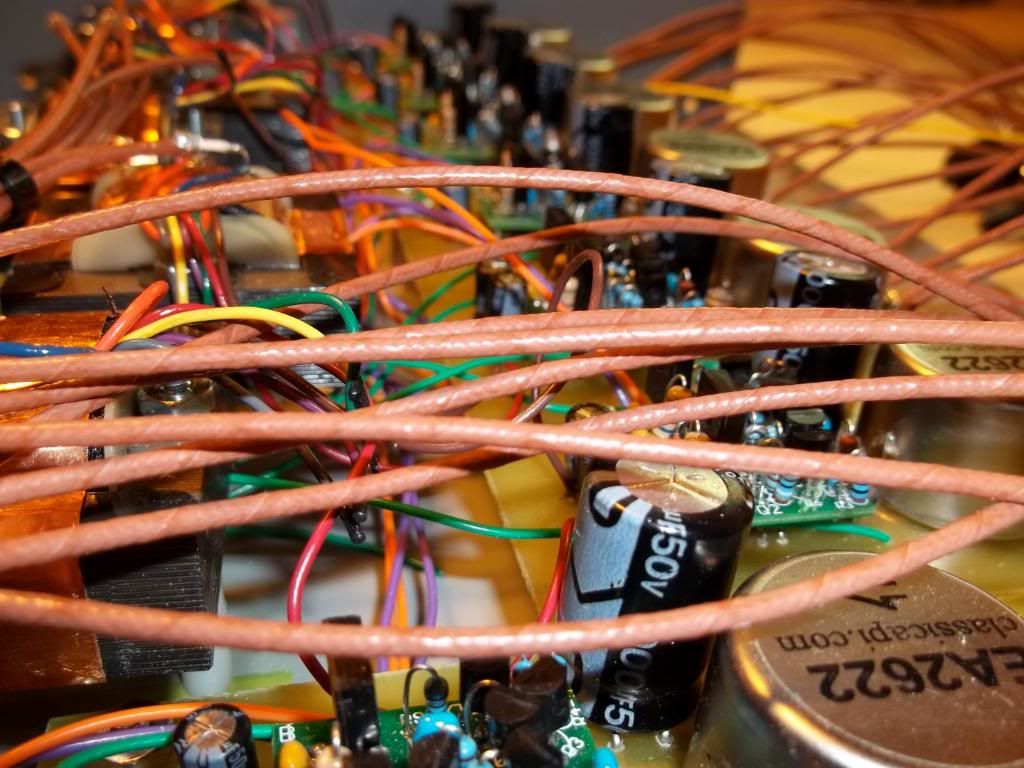
tight fit
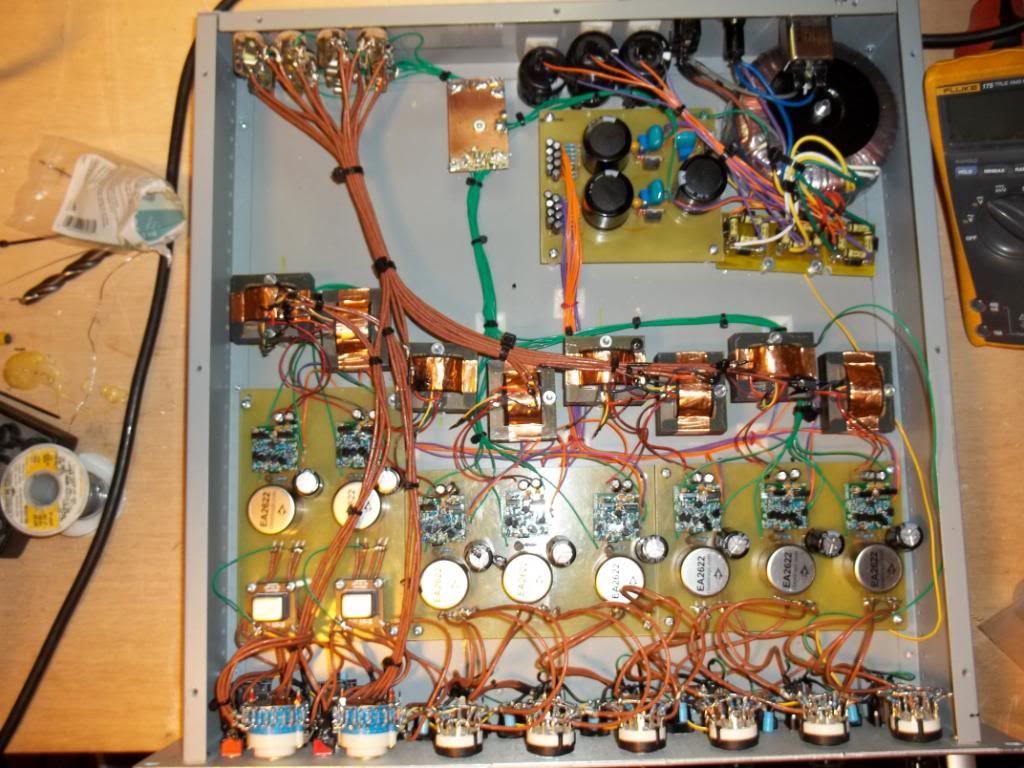
finished (I've since got smaller blue versions of the red knobs for the trim pots on the first two channels)
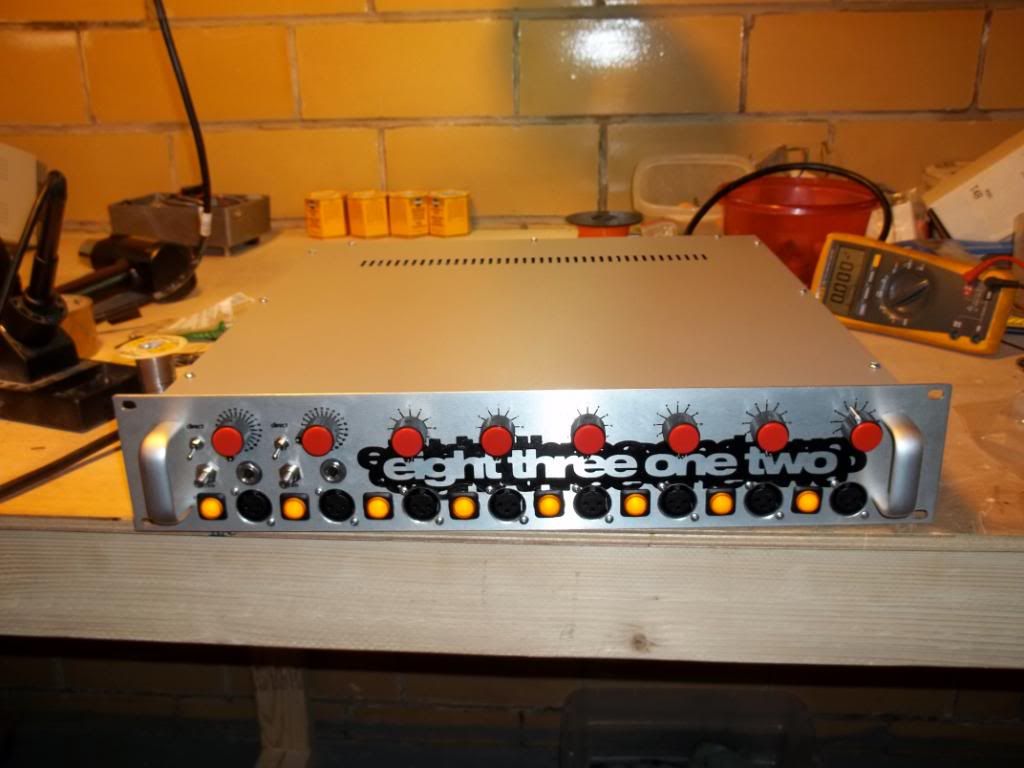